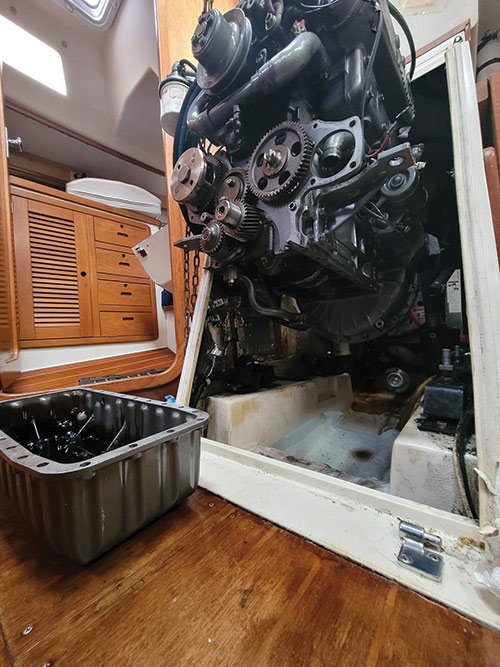
The question of whether to repair or replace an engine component, or the entire engine itself, is complicated. Answers vary greatly depending on the engine’s use over its lifetime, how well it has been maintained, and what is found during the diagnostic phase of trying to solve the problem.
I have worked with many folks who have spent a fortune on repairing what could’ve easily been replaced at a fraction of the cost, which brings the question, “When do we stop and just buy new?” Personally, I love the challenge of fixing what is broken. Yet despite my best intentions, that isn’t always realistically feasible. In my years working in this business, I have become keenly aware of the need for a point at which we pause, reassess what has been found, and to modify the game plan so the solution can happen without breaking the bank. I want to highlight some important aspects of this approach so that it might be considered and better understood by anyone in need of an engine repair.
When I first got started as a marine engineer and diesel mechanic, I only saw one small portion of the process. I was responsible for fixing the problem at whatever cost. I didn’t initially see or understand the financial side of that after the problem was fixed — I was nothing more than the technician on the floor turning the wrenches. It wasn’t until I began working as an independent contractor that my eyes were opened to how much things really cost, and whether people could actually afford the repairs or not. For larger scale projects, learning how to work with a reasonable budget has been beneficial to save the customer time and money.
The difficult reality is that, for many of us, marine diesels aboard our boats are older, potentially obsolete engines that may not be worth repairing. Having a competent professional who has this general knowledge can save the day when buying a boat or when deciding if an engine is worth dumping money into.
Example One: Prop Shaft
Let’s start with a simple example, one about which many friends and customers have shared their experiences: paying a pro to complete basic work on the propeller shaft of a vessel. This starts with separating the prop shaft from the coupling (to the reverse gear). Normally this process can be fairly quick; however when you are actually in the bilge trying to separate a flange that has been pressed onto the shaft for 10 years or more, this can be a daunting experience and take hours or even days. Access or lack thereof, of course, can make the process take even longer. If I am working on a sailboat with a 3-foot 1-inch propeller shaft and standard coupling, paying me to work at separating the pieces can be great if I can get the job done in a matter of 3-4 hours, but anything beyond that and it suddenly becomes cheaper to cut the shaft and coupling and buy an entire new assembly to save labor hours. The cost of a new stainless 3-foot propeller shaft and coupling with hardware can range from $400-$1,000 for the complete assembly. If you are paying to remove and repair the existing shaft, I have approximately 5 hours of labor (max) to try and get it apart before the cost to save the old pieces now has exceeded just buying all new pieces. I have heard horror stories of techs taking days to do this work without advising the customer that it is just cheaper to buy brand new and move on to the next part of the job.
Example Two: Full Rebuild
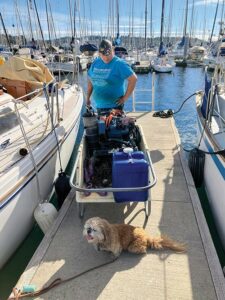
Now, let’s take that idea and apply it to rebuilding a smaller older diesel engine out of a sailboat. When folks come to me with a potential teardown and rebuild job, I will discuss the cost of a rebuild versus the cost of buying new. A lot of the time both of us land on simply replacing the engine as the cost of machining and other services can quickly add up, and that doesn’t include the labor to do the work.
For this example, I will use my boat: a Catalina 30. Over the years, Catalina 30s have used a variety of different engines. In the early days, Catalina used small raw water cooled engines such as the Atomic 4 or Universal 5411 (M15), before later moving to the fresh water cooled Universal M25, and eventually M25XP. When faced with a potential rebuild of one of these very common engines, I have to look at the availability of parts for the rebuild, whether the block and cylinder head can be serviced and machined, and the amount of labor to do this work. On the older raw water cooled engines I see nowadays, the block is usually very corroded and the cooling passages are partially or even completely blocked and unable to be cleared. While it is relatively easy to find a rebuild kit for a small Universal 5411 (M15), it suddenly becomes a challenge to service the block or cylinder head so it can perform like new for many years to come — and thus is a poor platform to rebuild.
Typically, raw water engines are the engines on which I find cracks or excessive corrosion damage, and the cost to re-machine or attempt to clean up these components to fit with the new parts can be very costly. A freshwater cooled engine (coolant cooled), on the other hand, is typically more worthy of a rebuild with new components, since its water jackets are typically fairly clean (if well maintained) so I can send the block out for service. Due to parts availability and the cost to source them (travel costs, shipping, time sourcing, etc.) this side of a large job can also become quite costly. A brand new 2-cylinder freshwater cooled engine costs $7,500-$9,500, so that becomes the working budget. If it looks like the cost to rebuild an old raw water cooled unit will exceed that, I will recommend buying new to save the time and effort on an obsolete unit. Afterall, a warranty and plentiful parts on that brand new unit can be nice to have. The only caveat has to do with potential installation expense for a replacement — a new engine may have different style mounts, require prop shaft or prop adjustment, different angles, or other work. So, be sure to understand what is required and make that part of your calculus.
Rebuilding a well maintained engine that is simply tired can also be absolutely worth it. Many marine diesels are designed with rebuild in mind, and have removable cylinder liners, among other things, to eliminate the prohibitive costs of machining. If I find the block or cylinder head to be in serviceable shape and the parts to do the work, then it can actually save money to simply teardown and rebuild with a good platform. Rebuild kits for smaller 2-3 cylinder engines are typically around $1,000-$1,500 and labor on a small to medium engine is about 25 hours or less. A properly rebuilt engine for the cost of $5,000-$8,000 is thus a reasonable cost compared to buying the brand new equivalent, however it is a delicate balance and the professional doing the work needs to be mindful of this so costs don’t go through the roof.
Considering your options ahead of time and working with a thoughtful mechanic who is familiar with the unit can really help when it comes to repairing or simply replacing. Many components on an engine can be torn down and replaced, however buying each piece individually and then paying the labor to rebuild can far outweigh the cost to just buy new. While I love to rebuild engines, sometimes, it’s not always reasonable financially. And the ability to say, “We need to stop!” before getting too deep into the project can be good!
Meredith Anderson is the owner of Meredith’s Marine Services, where she operates a mobile mechanic service and teaches hands-on marine diesel classes to groups and in private classes aboard their own vessels.