From the June 2022 issue of 48° North.
Working as a marine engineer and mechanic, I have seen and continue to see some of the worst DIY electrical jobs on boats, both recreational and commercial. Unlike residential situations, the marine world has few requirements for oversight or “inspections” of electrical work enacted by the owner, or even a professional.
The United States Coast Guard and American Boat and Yacht Council (ABYC) has created a list of standards for just about everything onboard your boat, electrical included. However, accessing those standards is nearly impossible unless you pay for them or work in the field as a professional. This is where many folks get into trouble following poor advice, wiring their boats like they would a house, or hiring a “professional” who knows little about why these standards are so important. Understanding some basics will help keep your engine running reliably, and will make your boat safer — but it might also lead you to seek out further information or resources before you start wiring things on the fly.
This article is centered around the electrical elements in your engine compartment, but many of these tips will spill into other systems onboard as well.
PROPER CABLE, CONNECTORS, HEATSHRINK
Issues with the electrical system are some of the most common problems on recreational vessels. Many fires have taken place due to poor electrical work, aging wiring, bad connections, and corrosion. The circuits in an engine compartment or engine room can be confusing — many appear as a rat’s nest, there is no proper color coding, abandoned wire is everywhere, or there are issues where connections have broken or chafed.
When wiring a circuit, it is critical to use proper multi-strand wire (preferably marine grade tinned copper) as solid strand cable will fracture with vibration over time. Connections should be crimped and never soldered for the same reason. Marine grade lugs and connectors are expensive, but worth the money so you only have to do it once — they will outlast your time on the boat! Heatshrink connectors or heatshrink for covering nylon connectors is also a good idea, and it is not just for the large cabling (starters and batteries). Small wires will disintegrate long before large cabling. Even if you think it’s a “dry location”…trust me, it’s not unless it is sealed in a watertight container.
CORROSION
Corrosion of wire is like cancer, it literally creeps in and does wicked things to cable underneath its sheathing. Corroded cable will NOT conduct electricity, making the cable’s ability to carry current a fraction of what it was built to carry. Imagine a 2/0 battery cable (about ¾-inch stranded cable) wiring an engine’s starter to the battery 5 feet away that is 50% corroded. 2/0 battery cable can carry about 200 amps comfortably in a 15 foot run. If it is 50% corroded, now it can only carry 100 amps. If the battery and starter are still functioning as intended, they will still try to pull 200 amps through that corroded cable — resulting in a lot of heat and possibly melting the cable or anything around it. Because it is installed in a “engine starting” application, ABYC and the USCG do not require fuses to protect this cable, meaning when the cable begins to melt, there is nothing to stop the entire run from becoming a giant fuse. If you remember nothing more about electricity, remember that corrosion causes resistance, resistance causes heat, and heat causes fire. Make sure to take the time to seal up connections with proper heatshrink connections (electrical tape is a no-no!) and spend the money for the tinned materials as they are much more corrosion resistant over a long period of time.
MAKING GOOD CONNECTIONS
An electrical circuit of any sort is only as good as its connections to and from the power source, and to the appliance it powers. Poor connections (corroded, loose, improper connectors, etc.) can lead to intermittent failure, but can also cause damage if ignored. The majority of engine circuits on recreational boats are DC (Direct Current) from a battery source. Most recreational DC battery systems are 12 volts or 24 volts. In the world of electricity, that is considered extremely low voltage. It is difficult to wire DC for long runs (more than 100-feet), as there is significant voltage drop. Imagine a hose with water running through it. Voltage is the potential for the water to be pushed through the hose — the potential for the water to do “work” in a sense. The physical movement of water through the hose is current. If you were to stand on the hose, you have created resistance in the circuit. Poor connections, loose connections, and corroded connections can cause a lot of resistance to the current flow within the “hose” or cable.
MOTORS
Onboard your boat, you may have a starter motor, windlass, bow thruster, stern thruster, refrigerator, or some other type of “motor” that requires DC power.
For example, let’s take a look at the starter motor on a diesel engine: this motor requires 12 volts to turn the diesel engine over to start. It takes a lot of amperage (current) to turn an engine over quickly enough to start. If I took a multimeter and tested the battery at its terminals getting 13.2 volts (charged battery), I should have almost the same voltage at the starter terminals on the engine because there should only be minor resistance from the cable run itself. If I were to loosen the connection at the battery or starter and test the starter terminals again, I may only find 11.0 volts. This poor connection has caused significant voltage drop. Corrosion or other damage to the cable or connectors will have the same effect, or compound the connection issue. Even if it is brand new, the starter will not have enough voltage to even try and turn the motor. You may hear the starter solenoid “click” but that is about it.
Electric motors are very finicky about voltage. If the voltage they are getting from the battery is below their minimum threshold (usually about 12 volts for a 12-volt system), they simply will not work. Many times I get called out to a “no crank no start” issue, where the owner has spent a lot of money on new batteries and a new starter only for it to be a voltage drop issue from a loose wiring connection or the battery cable being so corroded it can no longer carry the load anymore.
WIRE ORGANIZATION
In any electrical application, it is always desirable to have it arranged in a neat and tidy way so that it looks good. But, more importantly, it needs to be easy to work on, service, or diagnose.
Make sure all wiring is secured properly (every 18-inches or so) and that it is not rubbing against the engine where it can cause a dead short and start a fire. If wiring is rubbing, it needs to have some sort of chafe protection to keep it from becoming a problem. Remember, everything on a boat “moves” or vibrates when the engine is running, so keep that in mind when running new cable or replacing old stuff.
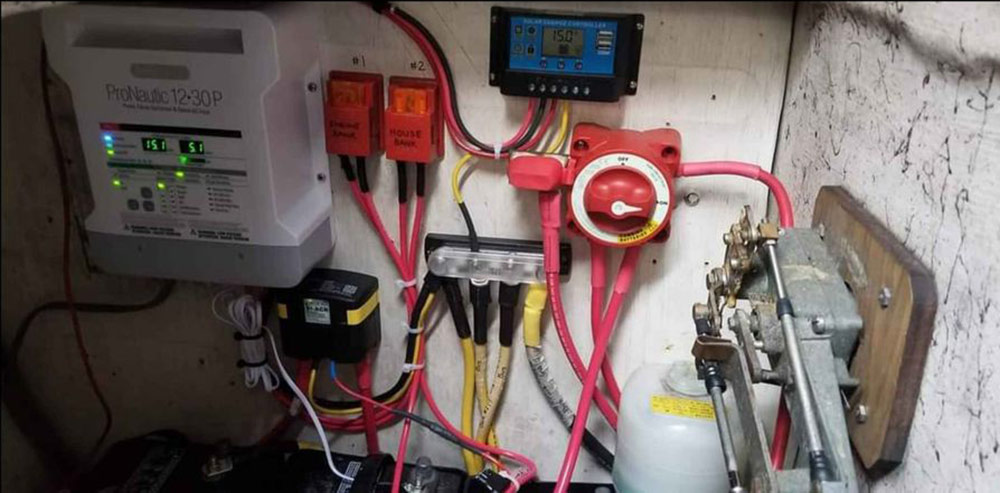
Taking the time to label circuits will make your life so much easier if there is a problem, but will also save you money if you are paying a professional to figure out the electrical system. Using terminal strips and buss bars are great tools for keeping batteries free of excessive connections. Marine-grade cable is a good investment as it is rated for higher temperatures and is oil resistant, unlike conventional automotive cable. In an engine compartment, keeping wiring away from fuel lines or oil lines is especially important, since you literally do not want to add fuel to the fire if something goes wrong!
Setting up safe, proper, functional electrical circuits is an important task. If you take the time to do it well, you most likely will not have to touch it again for many years. This is obviously only a cursory introduction to the principles of the electrical systems that make your engine and other components aboard work — so, take the time to research and ask questions about how to wire things properly. Enlisting the help of an expert who can guide you through ABYC and USCG requirements can enable you to continue this type of work safely and properly on your own. While there are many requirements to keep in mind, they are in place for a reason and can protect you if something goes wrong. Spending the extra time and money to do it right is well worth the safety and reliability it provides your boat and crew.
Meredith Anderson is the owner of Meredith’s Marine Services, where she operates a mobile mechanic service and teaches hands-on marine diesel classes to groups and in private classes aboard their own vessels.