This article was originally published in the April 2022 issue of 48° North.
In my last column (February 2022), we talked about oil’s function and filtration in a marine diesel engine, and noted that it is one of several essential types of filtration on a boat. Another, of course, keeps our diesel fuel working efficiently. Owners of vessels equipped with diesel engines face a variety of potential issues with the fuel we use in our modern engines, and maintenance of our fuel system is critical to a properly running and reliable engine while out on the water. Modern diesel fuel is subject to three main issues: water contamination, microbial growth, and particulate contamination.
WHAT IS THIS STUFF ANYWAY?

Before we get into the important aspects of diesel fuel system maintenance, let’s briefly discuss the makeup of modern age #2 Ultra Low Sulfur Diesel that we use in all on- and off-road applications today. What we call “diesel fuel” is really diesel fuel oil, and has been around for over 100 years. While it’s technically still an oil refined from crude oil and biomass materials, its general chemistry has been recently changed (in 1993, and again in 2006) by removing most of the sulfur content (from 500 to down to 15 parts per million or less) in response to EPA regulations for cleaner emissions.
Ultra Low Sulfur Diesel is diesel fuel oil that undergoes a process known as “severe hydrotreating” to remove sulfur. Less sulfur results in cleaner burning of the fuel and reduces the emissions of things such as Nitrous Oxides and diesel particulate matter (soot) into the environment, but also has some drawbacks relating to engine operation and fuel storage.
Hydrotreating fuel to remove excess sulfur also removes diesel’s natural lubricity (its capacity to reduce friction), and decreases the energy density of the fuel resulting in poorer fuel economy compared to the “old” stuff. Lower sulfur fuel also has a greater affinity for water and is subject to microbial contamination — making storage a challenge since fuel can now only be stored for approximately 6 to 12 months before burning the fuel may be an issue due to microbial growth. So how do we tackle these new problems related to our cleaner-burning fuel? Understanding what can and will happen will help us prevent problems before they arise.
WATER CONTAMINATION
Since we know that Ultra Low Sulfur Diesel has a higher affinity for water compared to older “traditional” diesel, it is something we need to pay attention to in our onboard fuel tanks. Water can enter the fuel in a variety of other ways as well, such as entering through a vent, as condensation in a partially filled tank, or simply washing the decks or accidentally mixing up our ports and filling the diesel tank with water.
Water is heavier than diesel fuel, and will sink to the bottom of the tank, where the pickup tube usually is. Water induces corrosion inside metallic storage containers, fuel injections pumps, or injectors. It is not easily compressible, and if small amounts make it through the filters and injectors or into the cylinders, it can actually damage piston and valve surfaces, or even hydro-lock components. Most vessels are equipped with two diesel filters, the first (nearest to the tank itself) is the primary fuel/water separator — its job is to separate the majority of the water out from the fuel before the fuel continues to the engine itself, as well as catching larger particulate like sand, dirt, and algae. The second is usually a fine filter to protect the fuel system components from smaller, but still damaging, particulates. It is very important to pay attention to the fuel/water separator, drain the water regularly, and watch the water level. If you notice more water than usual, there is a problem.
PARTICULATE CONTAMINATION
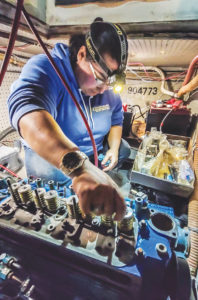
Diesel engines today have fuel systems with extremely tight clearances (<0.001 inch) that can be easily blocked by a tiny bit of dirt or debris. Efficient filtration is an absolutely critical component for a good-running diesel power plant. As mentioned above, many diesel power plants will have two fuel filters set up: a primary fuel/water separator and a secondary fine filter.
For the primary filter, I typically recommend a 10- or 30-micron filter. Racor brand filters are a common choice for boats, and are color-coded with an easy-to-identify micron rating. Installing too small a filter ahead of the engine can actually impede flow and starve the engine for fuel, so stay away from the 2-micron filters, unless you are trying to polish fuel and plan on changing filters often.
The secondary filter, typically mounted on the engine itself, can range from 2-10 microns and its job is to protect the fuel system components. A speck of dirt can severely damage an injection pump or block the nozzle of a fuel injector causing poor atomization (lots of smoke, hot spots, leaking injectors, etc). It is easy and comparatively cheap to change fuel filters regularly, so say on top of it to avoid further headaches.
MICROBIAL GROWTH
Also known as “diesel bug/algae,” microbial growth from bacteria and fungi is an issue all of us face on a regular basis in our tanks. Since modern diesel (and biodiesel even more so) is very hygroscopic — it absorbs moisture from the air — and the presence of water encourages this growth, microbes and algae can proliferate on tank walls or between the oil/water layers. Untreated fuel remains viable for about 6 to 12 months before signs of microbial growth appear, and outside factors such as heat can accelerate growth. The regular use of a biocide such as BIOBOR JF can kill this growth and allow it to be filtered out. Left untreated, this growth can become an infestation that clogs filters, causes fuel starvation, and damages fine components such as injection pumps or injectors.
While on-road vehicles in which the fuel is typically consumed within a few days or weeks occasionally deal with this issue, it is far more common on boats. Fuel on recreational and even commercial boats can sit for years and accumulate severe layers of growth that eventually lead an engine to run poorly, if at all.
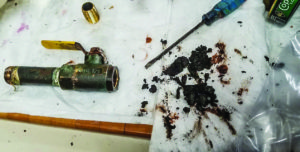
If growth is significant, it may be necessary to polish the fuel tank or fuel lines to stop the problem. This can be quite expensive, so considering the regular use of a good biocide at every fill up can prevent costly repairs. A biocide kills the growth, but leaves behind a grainy black particulate that the filters will catch so, again, make sure to change your fuel filters regularly.
The use of Ultra Low Sulfur Diesel today has yielded improvements in terms of emissions, but with every step forward comes a trade-off to watch out for. There are many good additive packages to assist in restoring fuel lubricity, zinc content, and protection from microbial growth that we can add to our tanks to prevent issues down the road and to protect our engines from corrosion and excessive wear and tear. Since our tanks of fuel typically don’t get consumed frequently, it is important to consider all the factors that could cause issues for us when we go to start up our engines this boating season. Understanding these factors will help us prevent those expensive repairs and frustrations down the road.